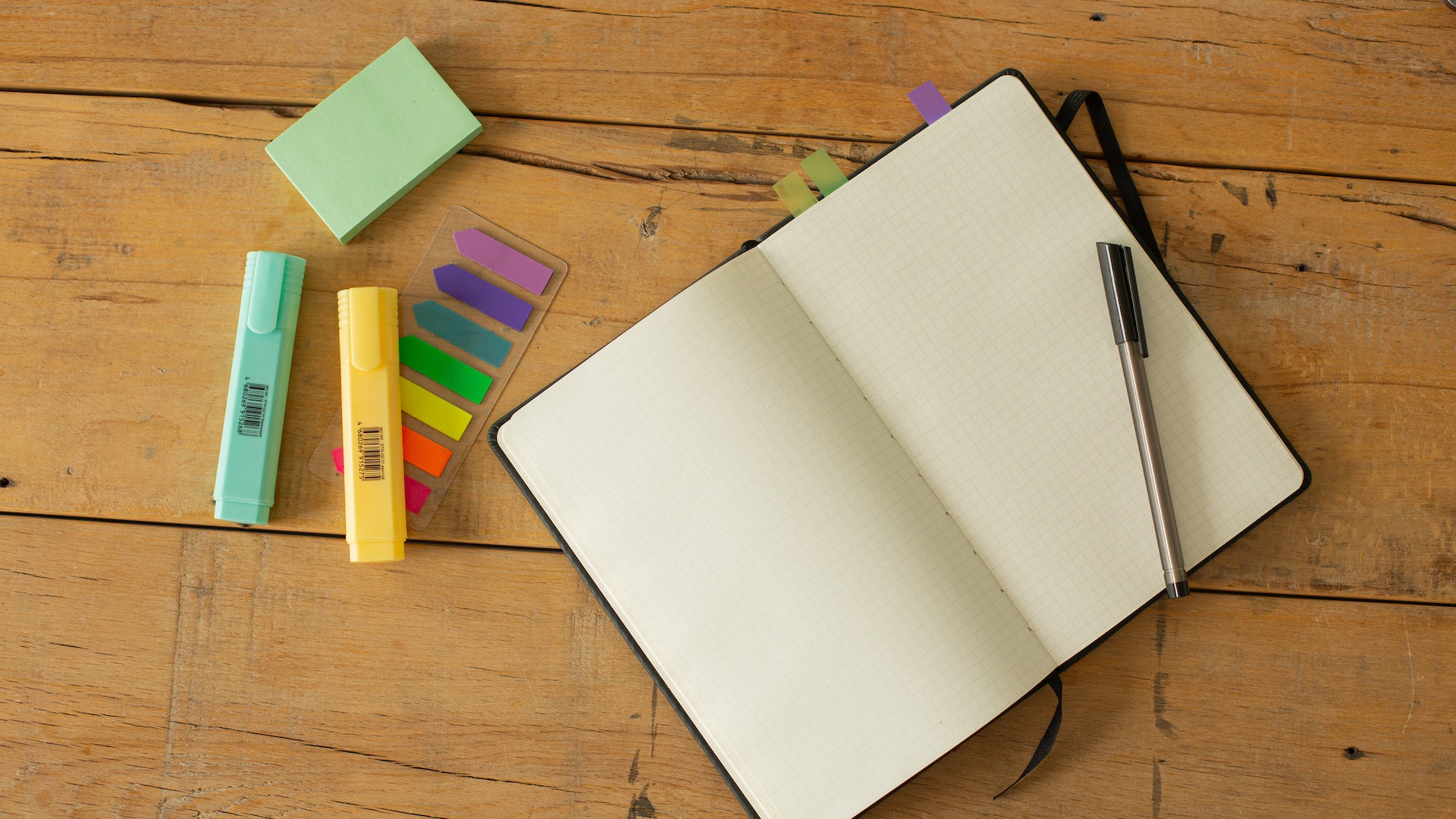
Organizing your workplace effectively with the 5S Method
Course overview
The 5S Training Certification Course is designed to provide participants with a comprehensive understanding of the 5S methodology and its implementation in the Workplace. The 5S concept is a system of organization and standardization that focuses on workplace efficiency, safety, and productivity.
The course is designed to cover each of the 5S steps in a logical order, starting with an introduction to the principles and benefits of 5S, progressing to the implementation of 5S in the Workplace, and then diving deeper into each of the 5S steps. Through this course, participants will learn the principles of 5S, how to apply them to their Workplace, and how to implement and sustain 5S in their organization.
The course will cover the five steps of 5S (Sort, Set in Order, Shine, Standardize, Sustain) in depth, providing participants with an understanding of the purpose and benefits of each step. The course will also cover the implementation of 5S in the Workplace, including conducting a 5S audit, creating a 5S plan, and implementing 5S in the Workplace.
Additionally, the course will cover the importance of standardization and visual management and the importance of sustaining 5S in the Workplace. The course will provide participants with the knowledge and skills needed to implement and maintain 5S in their Workplace, resulting in improved efficiency, productivity, and safety.
This course is suitable for professionals from all industries and backgrounds who are looking to improve the efficiency and productivity of their Workplace. The course is particularly relevant for managers, supervisors, team leaders, quality professionals, and anyone responsible for maintaining an efficient and organized work environment. The course is also beneficial for individuals who are looking to improve their organization and productivity skills. Additionally, the course is suitable for employees at all levels, as the 5S methodology can be applied to any work area and any work, regardless of the industry or field. This course is also beneficial for those looking to improve the efficiency and productivity of their Workplace, as well as those looking to improve the safety and quality of their Workplace.
Learning Objectives
- Understand the principles and benefits of 5S
- Learn how to implement the 5S methodology in the Workplace
- Understand the importance of standardization and visual management
- Learn how to conduct a 5S audit before and after implementation to measure the effectiveness of 5S
- Understand how to sustain 5S in the Workplace
Our Unique Training Methodology
The course is designed to be interactive and engaging, using a combination of lectures, group discussions, case studies, and hands-on exercises to ensure that participants can understand and apply the concepts of 5S in their workplaces. The course is designed to be a combination of theoretical and practical learning, allowing the participants to understand the concepts of 5S and apply them in real-life situations. The course will also enable the participants to collaborate and share their experiences with other participants, making it a unique learning experience.
Personal Benefits:
- Improved time management and productivity: By implementing the 5S methodology, participants will learn how to organize their work area and prioritize their tasks, resulting in improved time management and productivity.
- Better organization and efficiency in the Workplace: The 5S methodology focuses on organization and standardization, which leads to a more efficient and productive workplace.
- Increased job satisfaction: By working in a well-organized and efficient environment, participants will experience increased job satisfaction.
- Enhanced career development opportunities: By understanding and implementing the 5S methodology, participants will improve their skills and knowledge, leading to enhanced career development opportunities.
Organizational Benefits:
- Improved workplace safety: By implementing 5S, organizations can identify and address potential safety hazards, resulting in a safer workplace for employees.
- Increased efficiency and productivity: The 5S methodology focuses on organization and standardization, leading to improved efficiency and productivity in the Workplace.
- Reduced costs and waste: By implementing 5S, organizations can reduce costs by identifying and eliminating unnecessary waste and inefficiencies in the Workplace.
- Improved quality and customer satisfaction: The 5S methodology focuses on improving quality and customer satisfaction by ensuring consistency and standardization in the Workplace.
Training Medium
This Behavioral Interviewing training is designed in a way that it can be delivered face-to-face and virtually.
Pre-course Assessment
Refer to the email sent by us after you register for this course.
Course Modules
Module 1: Introduction to 5S
- Overview of 5S
- History and origins of 5S
- The five steps of 5S (Sort, Set in Order, Shine, Standardize, Sustain)
Module 2: Pre-Implementation 5S Audit
- Identifying areas for improvement
- Conducting a pre-implementation 5S audit
- Creating a 5S plan
- Implementing 5S in the Workplace
Module 3: Standardization and Visual Management
- The importance of standardization
- Creating standard work instructions
- Using visual management tools
Module 4: Post-Implementation 5S Audit
- Conducting a post-implementation 5S audit
- Measuring the impact of 5S on productivity and efficiency
Module 5: Sustaining 5S in the Workplace
- Creating a culture of continuous improvement
- Identifying and addressing challenges to 5S sustainability
- Maintaining and improving 5S in the Workplace
Module 6: Sort (Seiri)
- Understanding the importance of sorting and decluttering in the Workplace
- Identifying items that are not needed in the Workplace and disposing of them
- Implementing a sorting system to ensure items are in their proper place
Module 7: Set in Order (Seiton)
- Understanding the importance of organization and order in the Workplace
- Identifying the best location for items in the Workplace
- Implementing a labeling and identification system
Module 8: Shine (Seiso)
- Understanding the importance of maintaining a clean and safe workplace
- Implementing a cleaning schedule and system
- Identifying and addressing potential safety hazards
Module 9: Standardize (Seiketsu)
- Understanding the importance of standardization in the Workplace
- Creating standard procedures and work instructions
- Ensuring consistency in the implementation of 5S
Module 10: Sustain (Shitsuke)
- Understanding the importance of sustainability in the implementation of 5S
- Identifying and addressing challenges to sustainability
- Implementing a continuous improvement plan to maintain 5S in the Workplace
Module 11: 5S in Practice
- Case studies of 5S implementation in various industries
- Best practices and lessons learned from real-world examples
- Group discussion and brainstorming session on applying 5S in participants’ workplaces
Module 12: Final Exam and Certification
- Exam to test the knowledge acquired during the course
- Certification awarded to successful participants.